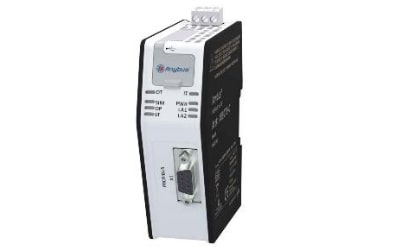
Exchange real-time factory-floor machine data with .NET based applications and keep integration work to a minimum with the Anybus .NET Bridge
As a user, you focus on defining and integrating an information model in your system while HMS’s Anybus technology handles the communication layer and message protocol.
On the OT side, you connect the PLC to the .NET Bridge through a function block and product definition files (GSD, GSDML, EDS, ESI). On the IT side, you add a C# .NET library to your application and use it to exchange data with the PLC.
The Anybus .NET Bridge acts as a bridge between a function block in a PLC and a .NET solution in a PC.
.NET Bridge comes with two different modes:
- A message mode where you set up data tags that should be exchanged between OT and IT and generate a corresponding product definition file and a function block for the OT side and a C# .NET library for the IT side. This reduces integration efforts on both sides.
- A streamer mode where a defined dataset is sent between the IT and OT side without any handshake, to maximise performance. Data need to be mapped manually in the PLC and in the .NET application. Available for PROFIBUS, PROFINET, and EtherNet/IP.
For the IT Specialist – .NET Programmer: Significantly reduced integration complexity!
- No need to understand industrial networks – Data from factory floor sent in an intelligible format
- IT style interface: customise names, receive events and post structured data via C# / .NET interface
- Automated configuration – system generates fully customised C# API (message mode)
- Names and data types according to parameter list agreed with PLC programmer
- PLC Simulator for testing/developing .NET solutions without PLC
- No configuration needs to be done inside the Bridge
For the Automation Specialist – PLC Programmer: Function block simplifies PLC integration
- .NET Framework knowledge is not required – The logic interface is a function block in the PLC
- Function blocks for TIA Portal are provided with the generated configuration (message mode)
- Automated configuration – system generates fully customized GSD file
- .NET Simulator for testing/developing PLC solutions without .NET
- If a bridge needs to be replaced, the .NET application will automatically setup the configuration, except the PROFIBUS Node address
Product Information
-
Creates a bridge between the logic in a PLC and a .NET solution in a PC
-
Two-way communication
-
Easy to configure and set-up
- Message size up to 251 bytes
- Possible to send messages in sequence up to transfer large amounts of data (up to 251 bytes x 65 535)
- PLC simulator to make it easy for the .NET programmer during development and commissioning
- .NET simulator available to make it easy for the PLC programmer during development and commissioning
- DIN-rail or wall mount options
- Streamer mode for high-performance applications for PROFIBUS, PROFINET, and EtherNet/IP
The parameters of the PROFIBUS Slave are defined in a spreadsheet configuration. A GSD is generated by the configuration generator together with function blocks.
- Allocates up to 244 bytes of I/O data
- Baudrate 12Mbit/s
- PROFIBUS uplink configuration via .GSD file
- Provided functional blocks for TIA Portal
- Connectivity via 1x female D-Sub9 connector
The information exchange between the Operational Technology (OT) side and the Information Technology (IT) side is made with messages defined in a spreadsheet template (Excel).
Up to 65535 different message types, with each message a max size of 251 bytes, may be defined. Each message type is identified with a unique ID number. The messages are sent in sequence over the same IO-data, which provides a very large total of data communication.
These message types are defined in a spreadsheet template (Microsoft Excel). The template is included in the configuration software together with the function blocks and product definition files (GSD, GSDML, EDS, ESI).
Using the spreadsheet, the Anybus .NET Bridge Code Generator creates C# files for the .NET programmer and PLC files for the PLC programmer. The configuration software also includes two simulators — a PLC simulator for the .NET programmer and a .NET simulator for the PLC programmer. A function block (provided by HMS) manages the handshake on the PLC side and provides an easy-to-use interface for the PLC programmer.
For applications where a minimum delay and maximum performance is required, the .NET Bridge can be used in streamer mode where data streams are exchanged directly without any handshake (PROFIBUS, PROFINET, and EtherNet/IP). In this mode, data need to be mapped manually in the PLC and in the .NET application.
Dimensions (L•W•H) |
110 x 35 x 101 mm or 4,33 x 1,38 x 3,98″ | |
Weight | 160g or 0,35 lbs | |
Operating temperature | -25 to +70 °C or -13 to +158 °F | |
Storage temperature | -40 to +85 °C or -40 to +185 °F | |
Power supply | 24 VDC | |
Current consumption | Typical 150mA | |
USB port | For firmware upgrades | |
SD memory card slot | Not used | |
PC TCP/IP connector | 2xRJ45 | |
Industrial network connector | (See the secondary network interface details above) | |
Galvanic isolation | On both BUS/Ethernet side | |
Mechanical rating | IP20, NEMA rating 1 | |
Mounting | DIN-rail (EN 50022 standard) or Wall Mount (optional) | |
Certifications | CE, CULUS, RoHS |
ORDER CODE |
AB9071 |
|
---|---|---|
Included components |
Anybus PROFIBUS to .NET bridge |
|
Guarantee | 3 years |
Book your product
We are fully committed to providing our customers with the very best products and customer service. We believe in going the extra mile to ensure that each customer is satisfied with our products and solutions. We have the experience and the reputation in the field to deliver the products customers need to expedite their projects and assure quality every step of the way.

Our expertise lies in establishing, maintaining, and leveraging plant data for business benefit. Through our innovative solutions, we work alongside you to streamline processes, enhance efficiency, and reduce costly downtime.
CONTACT US
Main: +27 (11) 548 9960
Sales: +27 (11) 548 9970
SOCIAL MEDIA
Copyright @2025 Industrial Data Xchange.
All rights reserved.