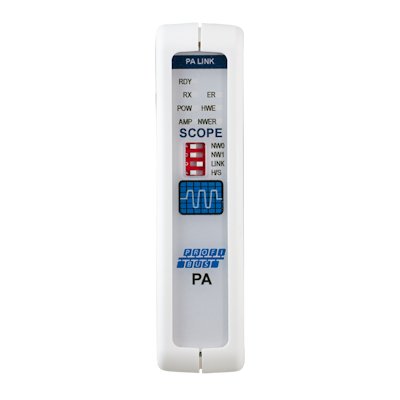
Seamless high-speed integration to PROFIBUS PA
The Anybus ComBricks is the first PROFIBUS-based automation system that unites repeaters and permanent monitoring in a web browser. With an evolving industry using more mixed architecture networks, users can integrate ComBricks into their PROFINET network via Osiris, allowing them to monitor everything from one single cross-platform.
The Anybus PROFIBUS PA link/coupler module enables seamless high-speed integration to PROFIBUS PA. It powers the attached PA devices and fully emulates them as DP devices on the backplane. Adjusted bus parameters are not required and therefore suitable for all DCS and PLC systems, even running on 12 Mbps.
The combined internal ProfiTrace and oscilloscope make this product extremely useful for remote maintenance over Ethernet. Jitter, noise, DC, DC voltage, bar graph and oscilloscope, it is all there and easy to access. The free CommDTM allows access to asset management tools over Ethernet.
ComBricks can carry 9 PA links and a RS 485 or Fibre Optic module. It can also be a customised mix of PA modules with other communication modules. The PA link provides a 500 mA current on a customisable bus voltage. The integrated PA termination is automatically activated when the module works as a power coupler. It is switched off in the monitoring mode.
It does not require configuration and operates the same way as regular ComBricks repeaters. In the web server, the behaviour on the PA side can be set, like retries (default 5) and the watchdog (default 3 seconds). This product can directly replace 3rd party Non-Ex PA couplers/links and can be used as a monitor behind existing 3rd party Non-Ex PA couplers.
Product Information
Distinctive features
PROFIBUS DP (on the backplane)
- 9.6 .. 12 Mbps
- Fully transparent
- No adjustments are required in Link mode
- Transmission speed detection: 9.6 kbps .. 12 Mbps (including 45.45 kbps)
PROFIBUS PA
- 10 .. 27 VDC customizable PA trunk voltage (Non-Ex)
- 500 mA trunk current
- 10 mA current consumption (in all modes)
- 32 (PROFIBUS PA specifications)
- 31.25 kbps PA signal
- 1900 m cable length (depends on trunk current)
- PA termination automatic (ON in coupler mode)
Web Server
- Oscilloscope images of connected devices
- Last, Min, Max bus signals
- Bar graph of connected devices
- DC current of the trunk and signal jitter
- Email on telegram errors and low bus signals
- Retry and Watchdog settings
Dimensions and weight
L x W x H: | 133 x 25 x 105 mm (including backplane, per module) |
Weight: | 133 g (excluding plug-able connectors, backplane and packing material) |
Mounting DIN-rail type | 35mm × 7.5mm (EN 50022, BS 5584, DIN 46277-3) |
Ambient conditions
Operating temperature range |
-20° … +60° Celsius (for mounting position see manual) -4° … 158° Fahrenheit |
Isolation class | IP 20 (IEC/EN 60529, DIN 40050) |
Backplane
PROFIBUS networks | 4 (set by dipswitches or web server) |
Module position | First 10 slots |
Modules |
Link mode: max. 9 PA modules and 1 DP repeater module Coupler mode: max. 9 PA modules and 1 DP repeater module Monitoring mode: max. 4 PA modules (4 backplane networks) |
Power supply | Provided through the backplane |
Typical backplane current | 350 mA (at 5.72 VDC) |
Max. backplane current | 550 mA (at 5.72 VDC) At this current consumption the module is switched OFF from the backplane. Occurs when the module is faulty, e.g. internal short circuit. |
Compatible backplane units |
101-200011, 101-200022, 101-200023, 101-200024, 101-200027 |
PROFIBUS PA power specifications
Trunk voltage | 10 to 27 VDC customisable PA trunk voltage (Non-Ex) |
Trunk current | 500 mA |
Current consumption | 10 mA (in all modes) |
PROFIBUS PA cable specifications
Cable lengths | Max. 1900 m cable length (PROFIBUS PA specifications) |
Wire diameter (for the screw terminals) | < 2.5 mm2 |
Wire type | Stranded or solid core |
Termination | ON when power supplied on the PA power connector |
PROFIBUS DP protocol specifications
Supported Protocols | DP-V0, DP- V1, DP-V2, FDL, MPI, FMS, PROFIsafe, PROFIdrive and any other FDL-based protocol |
Address | No bus address required |
Transmission speed | 9.6 kbps to 12 Mbps (including 45.45 kbps) |
Transmission speed detection | Auto detect (< 10 s detection and 50 s baudrate switchover time) |
PROFIBUS busparameters | No adjustments are required in Link mode |
PROFIBUS PA protocol specifications
Address |
Coupler mode: no address required Link mode: master on PA bus address 1 (fixed) |
Number of devices | 32 (PROFIBUS PA specifications) |
Baudrate PA bus | 31.25 kbps |
Oscilloscope specifications
AC PA voltage | 4 MS/s, resolution 7.5 mV, range -0.95 to 0.95 V |
DC PA voltage | 1 kS/s, resolution 75 mV, range -38 to +38 V |
DC PA current | 1 kS/s, resolution 1 mA, range 0 to 1024 mA |
Connector layout
2x PROFIBUS PA |
Plug-able screw connector, connectors 1 to 1, pitch 5.08 mm Pin PA- : 0 V Pin PA+ : 10 to 27 VDC Pin SH : Shield Pin I : Indirect Shield |
PA Power
|
Plug-able screw connector, pitch 5,08 mm Pin – : 0 V Pin + : 10 to 27 VDC Pin SH: Shield Pin SH is connected internally to the DIN rail with spring-loaded contact. The pin I is connected internally with 10nF/1MOhm to shield. |
Dipswitches
NW0 NW1 LEFT LEFT RIGHT LEFT LEFT RIGHT RIGHT RIGHT
LNK LEFT / RIGHT
H/S LEFT / RIGHT |
PROFIBUS Network
1 2 3 4
Link mode OFF / ON
Settings Hardware / Software
|
LEDs
RDY: Ready
|
The module is ready for operation (ON) |
RX: Receiving data | Receiving PA telegrams (blinking) |
HWE: Hardware error | Internal hardware error (contact HMS Technical Support) |
AMP: Amplitude error | No or bad telegrams on PA detected |
POW: Power error | PA signal too low or too high |
SNWER: Network error |
Over-current, noise, unbalance, DC-polarity Jitter, asymmetry, field device polarity Alarm values can be changed through the web server. |
Others
Head Station firmware | At least version 1.279 |
MTBF | 1165020 hours, at 30o Celsius, IEC TR 62380 |
Order Codes | 101-201610 |
Included Components | Anybus ComBricks, backplane socket |
Warranty | 1 year |
Book your product
We are fully committed to providing our customers with the very best products and customer service. We believe in going the extra mile to ensure that each customer is satisfied with our products and solutions. We have the experience and the reputation in the field to deliver the products customers need to expedite their projects and assure quality every step of the way.

Our expertise lies in establishing, maintaining, and leveraging plant data for business benefit. Through our innovative solutions, we work alongside you to streamline processes, enhance efficiency, and reduce costly downtime.
CONTACT US
Main: +27 (11) 548 9960
Sales: +27 (11) 548 9970
SOCIAL MEDIA
Copyright @2025 Industrial Data Xchange.
All rights reserved.